ChemResist - Sinterlining
Rotational Sinter Lining Applications
Chemical and pharmaceutical industry
Reactors and column plates, pipe-work, reduction adapters, vessels, tanks, valves, cylinders, filters, pump casings, vibration filters, centrifuge casings, filters, galvanizing baths, etc.
Foodstuffs industry
Hoppers, pipe-work, vessels, etc.
Semi-conductor technology
Pure water tanks, vessels for highly purified chemicals, exhaust air ventilation systems, solar energy, semi-conductor technology, etc.
Mode of Operations
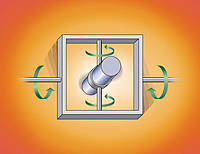
Rotational sinter lining is carried out by filling ultrapure thermoplastic granulate (with good flowing properties) into the hollow body, pipe or vessel to be lined. The object holder is heated and turned bi-axially so that a uniform layer thickness of molten granulate is applied seamlessly to the inner surface of the component.
Satisfied customers
- AllessaChemie
- BASF Ludwigshafen
- BASF PharmaChemikalien
- BASF Rudolstadt
- BASF Schwarzheide
- Bayer CropScience
- Bayer HealthCare
- Bayer MaterialScience
- Bayer Schering
- Bayer Technology Services
- Biochemie
- Boehringer
- Borealis
- Cabot
- Clariant
- Dow Rheinmünster
- DSM
- Dynamit Nobel
- DyStar
- Endress + Hauser
- Evonik
- Fluorchemie Dohna
- Haldor Topsoe
- Hoffmann-La Roche
- Ineos
- Infineon
- Jungbunzlauer
- KataLeuna
- Kemira
- Krohne
- Lanxess
- Lenzing AG
- Merck
- Momentive
- OMV
- PCK
- Robert Bosch GmbH
- Sachtleben Chemie
- Saltigo
- Sandoz
- Sanofi
- Siltronic
- Tectrion
- Uhde
- Vinnolit
- Wacker Chemie